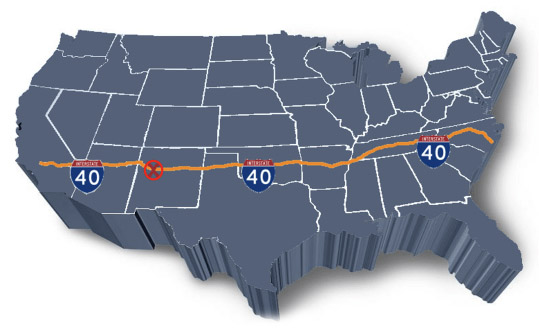
FHWA DEMONSTRATION
FINDS TREASURE UNDER THE INTERSTATE
Interstate 40 (I-40)
is a major east-west transcontinental highway running
through the southeastern and southwestern portions
of the United States from North Carolina to California.
Much of the pavement surfacing on I-40 within the
states of Arizona and New Mexico is so badly potholed
as to create a safety hazard for drivers. In response,
the New Mexico Department of Transportation (NMDOT)
recently closed down the eastbound lanes of I-40
near Gallup for three consecutive nights, entirely
shutting down for repairs all eastbound lanes of
the Interstate to all automobile and truck traffic,
a dramatic course of action in this day and age.
NMDOT spokesperson Delane Baros announced the following
day that this same section of highway would likely
have to be shut down again as the new repairs started
to fail almost immediately, and then adding, “The
reason being is because the bulk of the soil underneath
is clay, and then the subgrade is just completely
saturated with moisture.”
Following wet winter
weather conditions, some potholing and pavement
failure on I-40 is not abnormal, but the severity
of the problem this year is particularly troubling.
The Governor of Arizona recently held a press conference
to inform residents that millions of dollars will
be made available for repair work on Interstate
40 and the State of New Mexico issued a press release
announcing that they are conducting a study for
the reconstruction of I-40 all the way from Albuquerque
to the Arizona state line, a project of approximately
150 miles. The current estimated cost for that highway
improvement project in New Mexico is $830 million.
With Average Annual Daily Traffic (AADT) of 20,000
cars and trucks, 30% of which is truck traffic,
that works out to approximately four trucks and
ten cars per minute impacting the I-40 pavements
on an around-the-clock basis. At that traffic volume,
with both cars and trucks swerving in and out of
their lanes to avoid potholes and distressed areas,
these pavement failures are creating serious hazards
for road users and nightmares for the road maintenance
crews. Earlier this year, the local county sheriff
blamed potholes on I-40 as the cause of multiple
crashes and remarked that the pothole problem is
only getting worse. As history has proven, these
repairs will only function as temporary Band-Aids
until a more permanent and sustainable solution
is implemented to preserve the life of these pavements
for decades of safe, maintenance-free service, and
not just a few years.
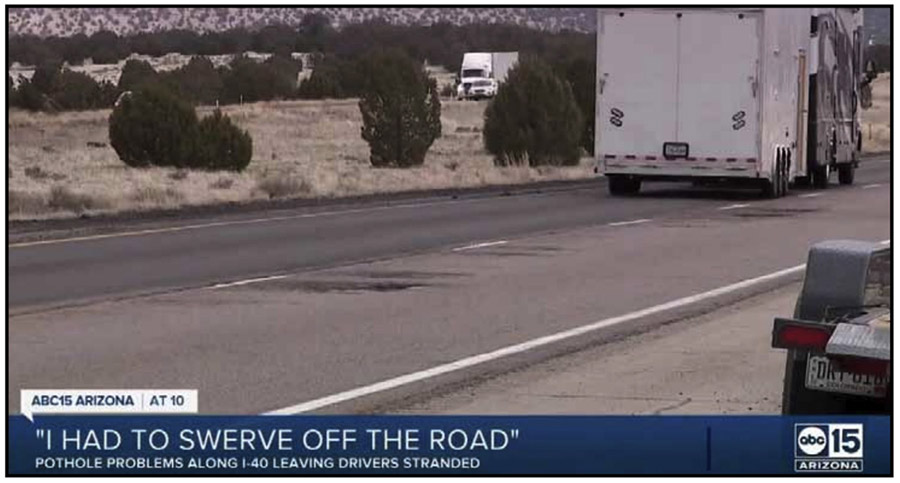
“The
reason being is because the bulk of the soil
underneath is clay, and then the subgrade is
just completely saturated with moisture.” |
TIMELY DISCOVERY
OF A SOLUTION
Timely then is the
recent discovery of the outstanding performance
of one segment of an I-40 reconstruction project
that incorporated innovative stabilization product
technology in two miles of its construction. As
recently confirmed by Mr. Eugene Hosteen, NMDOT’s
current Area Maintenance Supervisor in charge of
the maintenance of the I-40 pavements in this area
of the state, two miles of eastbound I-40 pavement
remain smooth-running and free of repairs after
23 years in service with “nothing more than
a fog seal applied” to the pavement surface
in recent years. While other I-40 pavements in this
area of New Mexico are currently potholed and have
been subject to complete reconstruction and numerous
repairs throughout the same period of years, the
trouble-free performance of this one section of
I-40 stands out as exceptional. Even more so, this
two mile segment of eastbound I-40 was historically
NMDOT’s worst area in the entire 150 mile
length of I-40 between Albuquerque and the Arizona
border. Last reconstructed in Year 2000, this two
mile section of I-40 featured use of advanced liquid
stabilization products with the encouragement of
the Federal Highway Administration (FHWA) New Mexico
Division Office. The project was designated as a
FHWA Demonstration Project, and involved the full-depth
reconstruction (complete removal and disposal of
asphalt pavement, aggregate base materials and saturated
soils below pavement elevation) of four miles of
I-40, identified as Milepost 93 to Milepost 97,
and included the two miles featuring the stabilization
of both the subgrade soils and aggregate base course
materials.
WORST I-40
PAVEMENT BETWEEN ALBUQUERQUE AND AZ STATE LINE
This four mile section
of Interstate reconstruction just happened to include
the two mile section of eastbound lanes that Will
Williamson, NMDOT’s Area Maintenance Supervisor
at that time, identified in his experience as “THE”
worst maintenance problem between Albuquerque and
the Arizona state line. The eastbound lanes of Interstate
40 that he was speaking about were located between
Milepost 94 and Milepost 96 (MP 94 – MP 96),
within the limits of the I-40 MP 93 – MP 97
reconstruction project. This section of I-40 transects
the Acoma Indian Reservation and runs through a
mountainous valley, much of which is underlain by
the El Malpais lava fields. One of the lava flows
runs parallel to the south side of I-40. This lava
flow interrupts the natural downslope drainage under
the highway and acts as a dam that traps water within
the silty clay and organic soils deposits located
immediately beneath the eastbound lanes. This unique
geology creates a worst case condition of trapped
groundwater directly underneath a pavement supporting
heavy truck traffic. Many other sections of I-40
are plagued with high groundwater, but the two miles
between MP 94 - MP 96 were considered by NMDOT Maintenance
as their very worst pavement problem. The worst
case.
PREDICTIONS
BASED ON CONVENTIONAL PAVEMENT DESIGNS
The MP 94 –
MP 96 section of eastbound I-40 had previously required
full depth reconstruction every 2 to 3 years, while
the westbound lanes constructed on more solid ground
were far less problematic. During reconstruction
of the eastbound lanes in Year 2000, NMDOT District
6 Engineer Larry Maynard commented that he anticipated
another full depth reconstruction project of this
same section would be required in less than three
years. Ron Clark, the Superintendent for contractor
WW Construction (WWC), predicted failure and reconstruction
within two years. He mentioned in a testimonial
letter that it was very difficult to work on top
of the native soils under the eastbound lanes that
were composed of “soft wet silt, clay and
dark stinking organic soils.” NMDOT and WWC
had worked together reconstructing many other sections
of I-40 between Albuquerque and the Arizona state
line during this same period of years, so both men
were speaking from extensive experience when making
these predictions.
Prior to year 2000,
when the I-40 MP 93 – MP 97 project was completed,
and during subsequent years, NMDOT was relying on
conventional pavement designs during reconstruction
of other sections of I-40, and basically increasing
the thickness of the asphalt pavement and the aggregate
base course layers as a continuing response to the
ongoing pavement failures. Their primary method
of dealing with localized subgrade failures during
these reconstruction projects was deep excavation
of saturated soils and replacement with virgin and
recycled aggregate materials reinforced with a combination
of geogrids and geotextile fabric products. Nothing
was done during these projects to treat the moisture
sensitive clay subgrades under the pavement structural
section. Consequently, none of these pavement reconstruction
projects have matched the extended performance of
the Eastbound MP 94 – MP 96 pavement installation
that incorporated base course materials and subgrade
soils treated with the EMC SQUARED System liquid
stabilizer products as part of the FHWA Demonstration
Project. The pavements constructed on top of these
EMC SQUARED stabilized subgrade and base course
layers were constructed over worst case ground conditions,
with an asphalt pavement section that was reduced
in thickness by two (2) inches, yet they remain
free of potholes and repairs twenty-three (23) years
later. The eastbound MP 94 – MP 96 pavements
will soon exceed the service life predicted by the
District Engineer and by the Construction Superintendent
by a factor of eight (8) times, with no sign of
failure currently anticipated.
INNOVATIVE
TECHNOLOGY SOLVES AN UNSOLVABLE PROBLEM
Potholes in highway
pavements are widely understood to be the result
of base and subgrade failures under the pavement,
failures generated by the presence of water in the
base materials and subgrade soils. Until measures
are taken to keep water out of the base and subgrade
layers, potholes and pavement failures will continue
to be a costly and dangerous problem. Ever thickening
layers of moisture and frost susceptible base course
materials will not eliminate the problem. Thicker
layers of asphalt pavement will not eliminate the
problem of water in the base course layer. Suction
and capillary attraction will continue to draw moisture
and pull ground water upwards into moisture susceptible
base materials, particularly when placed on top
of moisture susceptible subgrade soils. Geogrids
and geotextile fabrics may add tensile strength
and reduce the upward flow of clay particles via
capillary water into the base layer, but they do
nothing to keep the base material and the subgrade
soils dry and able to retain the strength that was
assumed in the pavement design. The addition of
cement and lime chemicals to base or subgrade layers
can increase the strength of the layer, but there
is no historical evidence that they eliminate the
moisture susceptibility problem itself, the problem
that continues to draw water in and saturate base
course and subgrade layers. For example, the I-40
MP 93 – 97 lanes reconstructed in year 2000
were previously constructed with asphalt pavement
placed on top of cement treated base (CTB) and that
pavement didn’t last three years. The EMC
SQUARED treatments instead keep the moisture content
in the base course layer and subgrade in a stable
state, without major fluctuations, while also functioning
as a moisture barrier impeding the upward and downward
movement of water within the pavement structural
section. The moisture barrier aspect of the EMC
SQUARED System stabilizer treatments is the clue
to understanding why the I-40 eastbound MP 94 –
MP 96 pavements, constructed on the EMC SQUARED
Subgrade and EMC SQUARED Base Course layers, can
remain smooth running and free of repairs 23 years
later, even with ground water trapped in the native
soils immediately below the stabilized subgrade
and base course layers.
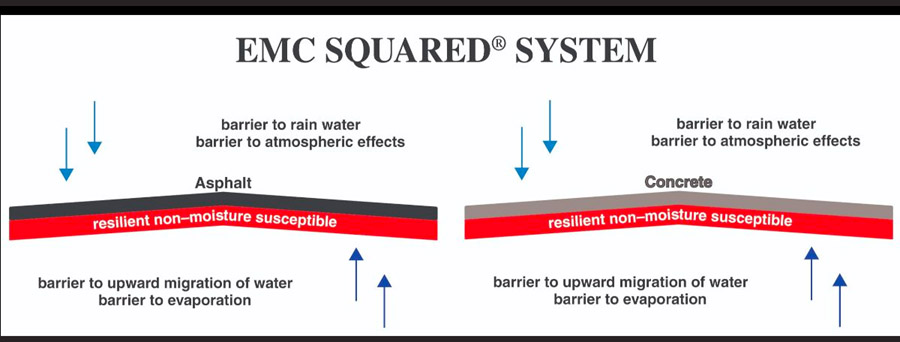
COHESIVE FORCES
BRIDGE UNDERLYING SOFT SOIL DEPOSITS
The exceptional
performance of freeway and highway pavements constructed
on foundation materials stabilized with EMC SQUARED
System liquid stabilizer products is not unique
to New Mexico. The solution to solving the frequent
failures of the I-40 pavements in New Mexico involved
utilization of the EMC SQUARED stabilizer products
to keep water out of the treated layers. After 23
years of trouble-free service, the long term benefits
of the EMC SQUARED stabilizer treatments for extending
pavement service life are now obvious, but also
noteworthy is the advantage the contactor achieved
by applying the EMC SQUARED treatments during construction,
giving themselves the ability to continue construction
uninterrupted by the delays that they would have
otherwise experienced while digging out and repairing
soft spots in their subgrade and backfilling with
layers of aggregate and geosynthetic reinforcement.
These unique stabilizer products also produce a
reaction in soils that rapidly generate increased
internal cohesive forces that help the stabilized
layer quickly bridge saturated soils below the subgrade.
Such bridging performance is unique to the EMC SQUARED
System stabilizer products.
MONITORING
OF FHWA DEMONSTRATION PROJECT
Ray Pederson, the
FHWA Area Engineer who was on site throughout the
construction of the eastbound lanes, was aware of
the particularly complicated geology underneath
this section of Interstate when he made the decision
to monitor on an ongoing basis the entire MP 93
– MP 97 project. Ray was a Professional Engineer
(P.E.) with a Materials Engineering background.
His intention was to evaluate whether the use of
the EMC SQUARED System liquid stabilizer products,
or the other chemical and mechanical stabilization
products used during this challenging highway construction
project, significantly contributed to extending
pavement service life. The variation in the underlying
ground conditions and the number of different methods
of stabilization made this a complicated monitoring
task, but Pederson was determined to make something
of value out of this Demonstration Project. To his
great credit, it was his 13-year monitoring effort
that finally led to the uncovering of a treasure
trove of information that otherwise would have remained
buried without his perseverance. The clues that
led him to his findings were being accumulated annually
by state crews operating high-speed profilers to
measure the smoothness, or the rate the pavement
was developing roughness in the form of International
Roughness Index (IRI) measurements. IRI measurements
are the international standard for evaluating highway
pavement performance. They provide the basis for
predicting the amount of service life remaining
in a particular segment of highway pavement.
UNCOVERING
THE CLUES TO FIND THE TREASURE
As FHWA Area Engineer
Pederson reported in his September 8, 2013, letter,
where he compared the performance of various different
chemical and mechanical stabilization measures used
during the construction of the MP 93 – MP
97 project, which is included as page 13 of summary
(https://stabilizationproducts.net/docs/18809.pdf),
nothing more than routine maintenance operations
were conducted during his 13 years of monitoring.
A thin bituminous treatment (Novachip) was applied
to the westbound lanes in 2008 and to the eastbound
lanes in 2009, and the following year an Open Graded
Friction Course was applied to the entire project
and adjacent sections of highway as a safety measure.
Pederson was onsite
during the 1999 – 2000 construction phases
of the I-40 MP 93 – MP 97 project. He was
aware of the fact that the eastbound lanes were
constructed on top of the worst case ground conditions
in this length of Interstate 40, while the westbound
lanes were constructed on a more solid native subgrade.
During construction, one mile of the subgrade soils
under the westbound MP 93 – MP 97 lanes had
been left untreated, with no chemical stabilizer
product applied. The soft spots in this one mile
section of subgrade were over excavated and replaced
with aggregate materials reinforced by a combination
of geotextile and geogrid products, but the subgrade
soils were otherwise left untreated. The remaining
three miles of subgrade soils were treated with
lime chemical. The second phase of the MP 93 –
MP 97 project used the EMC SQUARED liquid stabilizer
products during the construction of eastbound lanes
from MP 94 to MP 96. In the case of the construction
of the eastbound lanes, two out of the four miles
of subgrade were left untreated, with localized
repairs conducted on an as needed basis, in similar
manner as the untreated subgrade on the westbound
side.
STAYING ON
TASK AND FOLLOWING THE CLUES TO THE SOLUTION
Area Engineer Pederson
was aware that the different ground conditions underlying
the westbound and eastbound pavements were fundamentally
influencing the IRI test results. He concluded that
the monitoring program must incorporate the two
different starting points for the IRI measurements
and separate monitoring of the westbound and eastbound
lanes in order to properly measure and compare their
rates of deterioration over time, and not just their
initial smoothness at the time they were constructed.
He went on to collect the IRI monitoring results
over a period of ten years. He also made comparisons
with the different methods of subgrade construction
that were used under the westbound pavements and
the under the eastbound pavements, in each case
comparing pavement smoothness above the stabilized
subgrade to the pavement smoothness above the sections
of subgrade that were not chemically treated or
reinforced with the geosynthetic products. This
analysis allowed him to demonstrate that both the
lime treatment and EMC SQUARED treatments were clearly
beneficial in helping retain pavement smoothness
and prolong pavement service life. The first take
away that he achieved in analyzing the data from
this Demonstration Project was that chemical stabilization
of the subgrade soils under I-40 in this area of
New Mexico is highly cost-effective, in this case
using either lime or the EMC SQUARED System stabilizer
products.
Pederson was also
assigned as Area Engineer to two other NMDOT construction
projects on I-40 that were in progress during this
same period of years, and he reported that the smoothness
test results for the pavements constructed above
these chemically stabilized subgrades were superior
to those of the new segments of I-40 pavement being
constructed at both ends of the MP 93 – MP
97 project without use of chemical subgrade treatments.
The IRI data also confirmed over time that the EMC
SQUARED System applications were more effective
than lime treatment in preserving pavement condition
and prolonging service life, and once again more
effective than the geosynthetic products in preserving
pavement smoothness and service life. Using the
Theoretical Design Life calculations developed by
NMDOT to interpret the IRI data, Peterson was accurate
in his prediction that the EMC SQUARED System treatments
would be by far the most effective treatment measure
for extending pavement service life. For additional
perspective, the EMC SQUARED System treatments were
also the lowest cost to purchase and fastest to
install.
LESSONS TO
BE LEARNED
Given the current
pothole epidemic that is seriously endangering the
safety of I-40 highway users in Arizona and New
Mexico, along with the revelation by NMDOT that
they recognize pothole pavement failures are caused
by saturated clay subgrades, the conclusion could
be drawn that the Department of Transportation should
expand approval and use of stabilizers products
that counteract the movement of water into highway
subgrade soils. As proven by this FHWA Demonstration
Project on Interstate 40, there is an affordable
alternative to short-lived conventional construction.
Interstate Highways can be designed with moisture-resistant
foundation materials that have the year-round solid
support that asphalt pavements require to provide
decades of pothole-resistant service.
VIDEO TOUR
OF EASTBOUND I-40 MP 94 - MP 96 ABOVE EMC SQUARED
STABILIZED SUBGRADE AND BASE COURSE
Take a one minute
video tour of the eastbound MP 94 – MP 96
segment of Interstate 40. This pavement was constructed
on top of subgrade and base course layers treated
with the EMC SQUARED System products to keep water
out of the base course materials and subgrade soils.
This section has been 23 years in service over worst
case ground conditions without need for repair or
reconstruction. The video footage was taken in April
2023, in the midst of the current epidemic of hazardous
potholes that have made other sections of Interstate
40 in both Arizona and New Mexico truly life-threatening
to drive, and that have caused repeated shutdowns
of the Interstate for pothole repairs.
FOR AN EVEN
DEEPER DIVE
For a deeper dive
into the related construction history and the monitoring
results of the 13 year study conducted by the FHWA
Area Engineer, visit https://stabilizationproducts.net/docs/18809.pdf
NOTE: If you are interested
in the studies conducted by independent soil and
pavement materials testing laboratories, whose results
give evidence as to the how and why the performance
of EMC SQUARED System stabilizer products prolonged
the service life of the FHWA Demonstration Project
on Interstate 40, look for the next newsletter coming
soon. In case you missed one, earlier newsletters
describing laboratory and field tests, as well as
projects in North America can be found here: https://stabilizationproducts.net/newsletters.html
For a summary report
on other smooth running highways built on EMC SQUARED
subgrades constructed above deep deposits of expansive
clay soils, visit
https://stabilizationproducts.net/docs/18791.pdf
and
https://stabilizationproducts.net/docs/18468.pdf